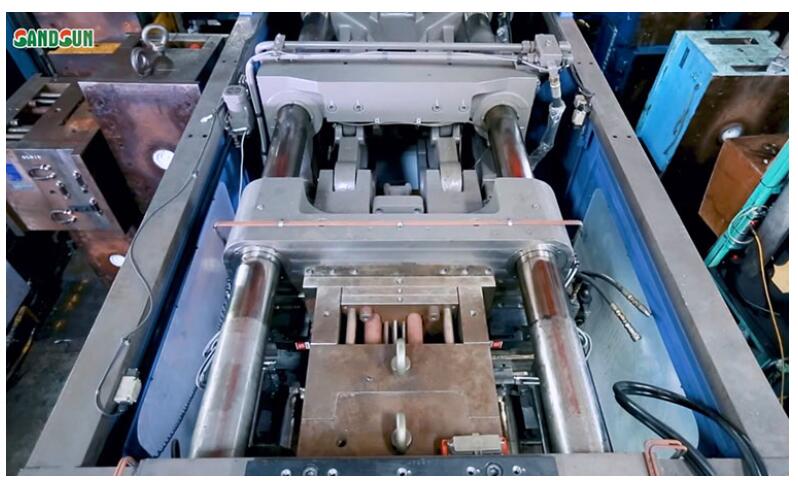
SEMD快速换模——降低时间和成本
针对上述问题,实施“快速换模”是*好的解决方案。这种方法在欧美企业中早已使用。在日本,由于TPS(丰田生产系统)的理念,汽车行业实施了SMED(单分钟更换模具),这与“快速模具/模具更换”的理念相同;甚至大多数汽车制造商都为此概念制定了SOP作为标准。
那么如何实现快速换模,使注塑模具换模流程**呢?您必须了解以下 5 个关键提示。
完善的前期工作计划
换模过程*般可分为:停机前操作、停机中操作、停机后操作。
停机前作业如:换模人员调度、换模工具准备、模具运输...等。
停机时的操作如:模具的拆卸/固定、模具定位、水/油/电路接管操作...等。
停机后的操作如:刀具归位、模具归位、地面清洁...等。
完美的规划就是尽可能减少停机期间的工作时间,并不断改进停机前后的操作流程,使整个换模过程尽可能减少浪费。
标准化并简化换模操作
停机前/停机后操作的优化可通过标准化、简化的方式进行,例如:标准化模板厚度尺寸(模芯无需标准化),以方便模具快速定位和固定、交通便利等优势;或将换模工具和模具放置在固定位置,以减少寻找时间。
使用快速换模系统协助换模过程并减少停机时间
停机期间的工作可以使用快速换模系统来减少停机时间。例如,过去模具是通过螺钉固定的。现在,使用液压夹具或磁力板来代替螺钉,这将大大减少在机器中拆卸或固定模具的时间。利用定位销和标准模具底板,*次完成模具定位过程,无需反复调整定位。使用这些快速换模系统不仅可以规范停机期间的操作,还可以为员工提供更安全的换模过程环境。
延伸阅读:液压夹紧系统 VS 磁力夹紧系统
培训人员按照SOP(标准操作程序)更换模具
规范停机前后及停机期间的操作,并制定SOP。然后培训模具安装人员按照SOP进行工作。不仅可以轻松地向新员工传授换模操作,而且无需担心经验丰富的员工失去技能。换模流程标准化后,任何员工都可以通过SOP轻松完成换模工作。
逐步向换模过程全自动化的目标迈进
当所有操作程序都标准化后,就可以进*步使用机器人或换模车来进行全自动换模过程。只需轻轻*按,无论停机前后、停机期间,机器均可全自动完成所有过程。
如今,汽车追求自动驾驶,机器追求全自动生产,工厂要走向熄灯工厂。无论是五金冲压生产线还是注塑生产线,不断改进生产技术,将不必要的浪费控制在*低水平的企业,将不断向着全自动生产的目标迈进。那么,这些公司就有资格谈持续经营。